Eliminate zamak and aluminum
die-cast scraps with Formula Foundry
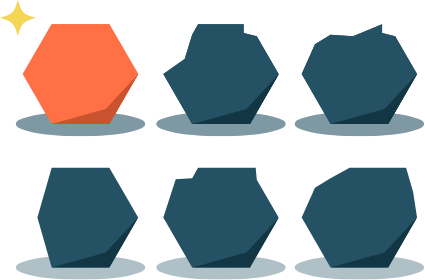
The problem of waste
In today's world of foundries, only 30% of the potential of the machines is exploited, because there are no tools capable of making those who design the mold and those who regulate the press communicate. In some cases there is a high probability of having a high waste, uncontrolled or erratic production.
In Italy alone there are more than 800 foundries producing aluminium castings (about 90%) and zamak (about 10%).
Problems can often occur in the management of the production process.
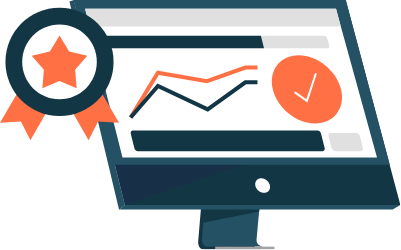
Get to know Formula Foundry
Formula Foundry S.r.l. is an innovative research and development startup, which aims to:
- Create skills for people working in the diecasting sector with training activities
- Design and create production calculation, regulation and monitoring systems based on scientific rules
The Formula Foundry software is based on a patented process after years of research and development, and allows to design, regulate and monitor the die casting process.
Formula Foundry: the original software to design, manage, regulate and monitor the production of die casting machines
Formula Foundry Cloud is global:
you can manage your project and adjust your press
in 7 different languages:







The advantages
Reduction of scrap
and molds proofing
Produce low-waste sample and monitor the process to maintain consistent quality during final production is possible.
Reduction of energy
and production costs
Improved efficiency of the foundry allows to reduce its energy and production costs, thus increasing turnover.
Ease of use
Smartphones, tablets and objects of simple and daily use can work in a coordinated manner with the presses to regulate the process without losing time.
Process stabilization
You can autonomously adjust and monitor the process directly from the machine parameters.
Increase in production speed
The production speed is increased by using the optimal solution suggesting.
Increase in quality
Greater precision allows to increase product quality and reduce part cost.
The origins of Formula Foundry
Formula Foundry’s idea was born from Roberto Camerin, a twenty-year expert in the sector, with years of experience in the die casting’s field.
Over the years, thanks to his activities directly in the field and to the technical and scientific study of process problems, he has developed the tool allowing to optimize the die-casting process on the basis of mathematical calculations.
The first activities successfully optimized led him to open his first blog dedicated to zamak, Zama Scarto Zero, followed by the second dedicated to aluminum, Alluminio Scarto Zero.
In March 2020, the process developed by Roberto Camerin obtains a patent for an industrial invention, and the development of the software that takes the name of Formula Foundry begins.
In February 2022 Formula Foundry becomes an innovative startup in die casting’s field, in which it carries out research and development, with the experience of 4 engineers who are experts in process, programming and software, management of companies and die casting applied to the foundry.
About us
Numerous satisfied customers already use Formula Foundry, implementing the process for optimizing the production processes of their foundries.
Many have joined the training program for personnel in the manufacturing’s processes fields, design or quality control.